TIÊU CHUẨN VIỆT NAM
TCVN 1992 – 77
HỘP GIẢM TỐC THÔNG DỤNG – YÊU CẦU KỸ THUẬT
Reducing gear of general pyrpose – General technical requirements
Tiêu chuẩn này áp dụng cho các hộp giảm tốc thông dụng sau đây:
– Hộp giảm tốc bánh răng trụ một, hai và ba bậc có các trục không di động với khoảng cách trục của bậc chậm ac ≤ 710 mm;
– Hộp giảm tốc hành tinh bánh răng trụ một và hai bậc với bán kính cần của bậc chậm R ≤ 200 mm;
– Hộp giảm tốc bánh răng côn một bậc với đường kính vòng đỉnh của bánh răng da ≤ 630 mm;
– Hộp giảm tốc bánh răng côn – trụ hai và ba bậc với khoảng cách trục của bậc chậm ac ≤ 630 mm;
– Hộp giảm tốc trục vít một bậc với khoảng cách trục a ≤ 250 min;
– Hộp giảm tốc trục vít – bánh răng trụ hai bậc với khoảng cách trục của bậc chậm ac ≤ 250 mm.
1. YÊU CẦU KỸ THUẬT
1.1. Hộp giảm tốc phải được chế tạo theo các bản vẽ đã được xét duyệt phù hợp với yêu cầu của tiêu chuẩn này và các tiêu chuẩn khác về hộp giảm tốc.
1.2. Hộp giảm tốc phải sử dụng được trong các điều kiện sau đây:
– Tải trọng cố định hoặc thay đổi theo một chiều hoặc đảo chiều;
– Làm việc liên tục hoặc nghỉ theo chu kỳ;
– Trục có thể quay được mọi chiều như nhau;
– Số vòng quay của trục nhanh của hộp giảm tốc bánh răng trụ và hộp giảm tốc bánh răng còn – trụ khi ac ≥ 315 mm; hộp giảm tốc bánh răng côn khi da ≥ 400 mm và hộp giảm tốc trục vít:
đến 1800 vòng/phút;
các hộp giảm tốc khác đến 3600 vòng/phút.
Chú thích: Khi sử dụng hộp giảm tốc có số vòng quay của trục nhanh lớn hơn 1500 vòng/phút thì hộp giảm tốc được cung cấp theo những đặc tính kỹ thuật đã được thỏa thuận giữa nơi chế tạo và nơi đặt hàng.
– Vận tốc vòng của truyền động bánh răng trụ đến 20 m/s; của bánh răng côn đến 16 m/s;
– Nhiệt độ của môi trường xung quanh đến 500C;
– Tránh được bụi;
– Môi trường không ăn mòn;
– Độ ẩm khi nhiệt độ 200C đến 95%.
1.3. Khối lượng tương đối
của hộp giảm tốc nằm ngang có vỏ bằng gang, bằng tỷ số giữa khối lượng của hộp giảm tốc (kg) và mô men xoắn cho phép trên trục chậm trong quá trình làm việc với tải trọng không đổi MT tính bằng Nm (hoặc KGm). Trị số khối lượng tương đối
của hộp giảm tốc được quy định trong phụ lục tham khảo tiêu chuẩn này.
1.4. Tỷ số truyền U và số vòng quay của trục nhanh nN để quy định khối lượng tương đối trên hình 1, theo chỉ dẫn trong bảng 1.
Kiểu hộp giảm tốc
|
U
|
nN
|
Bánh răng côn (U = 1 đến 2,8)
Bánh răng côn – trụ ba bậc
Bánh răng côn – trụ hai bậc
Trục vít – bánh răng trụ hai bậc
Bánh răng côn (U = 3,15 đến 5)
Trục vít không vạn năng (MT ≥ 1000 Nm)
Bánh răng trụ hai bậc dạng không đối xứng
Bánh răng trụ ba bậc
Bánh răng trụ hai bậc dạng đối xứng
Hành tinh hai bậc
Bánh răng trụ hai bậc đồng trục
Trục vít vạn năng không có bộ phận làm nguội (MT ≤ 2000 Nm)
Hành tinh một bậc (U = 3,15 đến 12,5)
Hành tinh một bậc (U = 50 đến 10 000)
Bánh răng trụ một bậc
|
1
125
25
125
5
25
25
125
25
25
25
25
5
125
5
|
500
1500
1500
1500
500
1000
1500
1500
1500
1500
1500
1500
1500
1500
1500
|
Chú thích: Hộp giảm tốc thẳng đứng và có trục chậm thẳng đứng cho phép có khối lượng tương đối lớn hơn đến 10% khối lượng của các hộp giảm tốc tương ứng trên hình vẽ.
1.5. Hộp giảm tốc phải chịu được tải trọng công xon hướng tâm Pc tại điểm giữa của phần nhô ra khỏi hộp của trục chậm, không nhỏ hơn các giá trị sau đây:
– Đối với hộp giảm tốc hành tinh với tỷ số truyền i ≤ 12,5 và các hộp giảm tốc bánh răng một bậc khác:
Pc = 125
khi MT tính bằng Nm.
Hoặc Pe = 40
khi MT tính bằng KG m.
– Đối với hộp giảm tốc còn lại:
Pc = 250
khi MT tính bằng Nm.
Hoặc Pc = 80
khi MT tính bằng KG m.
1.6. Trục nhanh phải nối được với động cơ bằng khớp nối hoặc truyền động dây đai.
1.7. Kết cấu của hộp giảm tốc phải sao cho dầu không chảy ngoài vỏ hộp và bùn, nước không xâm nhập vào trong hộp.
1.8. Trên vỏ hộp giảm tốc phải có kết cấu để móc khi vận chuyển và lắp đặt.
1.9. Trên vỏ hộp giảm tốc có chiều dài lớn hơn 1000 mm phải có những bề mặt gia công nằm ngang để hiệu chỉnh hộp giảm tốc khi lắp đặt.
1.10. Kết cấu của kích thước chỉ dầu và hệ thống dầu bôi trơn phải sao cho không bị hư hỏng khi vận chuyển.
1.11. Trong tổ chức sản xuất chuyên môn hóa, tuổi thọ của hộp giảm tốc làm việc lâu dài với tải trọng không đổi không được thấp hơn:
– Đối với hộp giảm tốc bánh răng 36 000 h;
– Đối với hộp giảm tốc trục vít 20 000 h.
Ở chế độ làm việc khác, thời gian sử dụng của các hộp giảm tốc bánh răng không thấp hơn 10 năm và hộp giảm tốc trục vít không thấp hơn 5 năm.
1.12. Tuổi thọ của ổ trục trong hộp giảm tốc được chế tạo hàng loạt làm việc với tải trọng không đổi có tỷ số truyền U và số vòng quay của trục nhanh nN theo chỉ dẫn trong bảng 1, không được thấp hơn:
– Đối với hộp giảm tốc bánh răng 10 000 h;
– Đối với hộp giảm tốc trục vít 5 000 h.
Khi hộp giảm tốc làm việc với số vòng quay ấy và tỷ số truyền bé nhất thì tuổi thọ của ổ trục không được thấp hơn 1500 h.
Chú thích: Những chỉ tiêu về tuổi thọ quy định trong các điểm 1.11 và 1.12 được bảo đảm với xác suất 90 %.
1.13. Trong tổ chức sản xuất chuyên môn hóa hệ số sử dụng kỹ thuật của hộp giảm tốc không thấp hơn:
– Đối với hộp giảm tốc có mômen MT đến 500 Nm là 0,98;
– Đối với hộp giảm tốc có mômen MT trên 500 đến 8000 Nm là 0,97;
– Đối với hộp giảm tốc có mômen MT lớn hơn 8000 Nm là 0,95;
Chú thích: hệ số sử dụng kỹ thuật Kt của hộp giảm tốc được tính theo công thức:
Kt = 
trong đó:
Tt – tổng số thời gian đã làm việc của hộp giảm tốc;
Ts – tổng số thời gian ngừng làm việc để sửa chữa;
Td – tổng số thời gian ngừng làm việc để bảo dưỡng kỹ thuật.
1.14. Sai lệch giới hạn của kích thước danh nghĩa từ đường trục của trục chậm đến mặt đế của hộp giảm tốc không được vượt quá các giá trị sau đây:
Kích thước danh nghĩa, mm
|
Sai lệch giới hạn
|
đến 50
|
– 0,4
|
trên 50 đến 250
|
– 0,5
|
trên 250 đến 630
|
– 1,0
|
trên 630 đến 1000
|
– 1,5
|
1.15. Sai lệch giới hạn cửa kích thước danh nghĩa từ tâm của lỗ lắp bulông nền đến mặt phẳng trung bình của hộp giảm tốc và đến đường trục của trục chậm không vượt quá +0,17 (D – d), trong đó D là đường kính danh nghĩa của lỗ lắp bulông nền; d là đường kính doanh nghĩa của bulông nền.
1.16. Độ không song song giữa đường trục của các trục quay và mặt đế của hộp giảm tốc:
– Khi đế liền với vỏ hộp, không vượt quá 0,1 mm trên chiều dài 100 mm;
– Khi đế rời, không vượt quá 0,3 mm trên chiều dài 100 mm.
1.17. Độ không phẳng của mặt đế:
– Khi đế liền với vỏ hộp, không vượt quá 0,05 mm trên chiều dài 100 mm;
– Khi đế rời không vượt quá 0,2 mm trên chiều dài 100 mm.
1.18. Khi chế tạo hàng loạt, cấp chính xác của truyền động bánh răng trong hộp giảm tốc không thấp hơn 8 – 7 – 7 L3 theo TCVN 1067-71, TCVN 1686-75, TCVN 1687-75. Bánh răng có đường kính lớn hơn 500 mm cho phép chế tạo với cấp chính xác 8L3 theo TCVN 1067-71, TCVN 1686-75 và TCVN 1687-75.
Cấp chính xác của truyền động bánh răng Nôvicốp và truyền động trục vít Glôbôít trong hộp giảm tốc theo tài liệu kỹ thuật đã được xét duyệt của cơ sở sản xuất.
1.19. Khi chế tạo hàng loạt, độ nhẵn bề mặt làm việc của răng:
– Trục vít không thấp hơn
8;
– Bánh răng nhỏ có môđun đến 5 mm – không thấp hơn
7, có môđun lớn hơn 5 mm – không thấp hơn
6;
– Bánh răng lớn có môđun đến 5 mm – không thấp hơn
6, có môđun lớn hơn 5 mm – không thấp hơn
5;
Đối với trục răng mà đường kính vòng đỉnh của đoạn có răng nhỏ hơn đường kính của ngõng trục kê đó cho phép độ nhẵn bề mặt làm việc của răng thấp hơn một cấp so với quy định trên.
Độ nhẵn bề mặt làm việc của răng bánh răng Nôvicốp, trục vít và răng bánh vít của truyền động trục vít Glôbôit trong hộp giảm tốc theo tài liệu kỹ thuật đã được xét duyệt của cơ sở sản xuất.
1.20. Bánh răng được chế tạo từ phôi đúc và quay với số vòng quay lớn hơn 500 vòng/phút phải được cân bằng. Giá trị giới hạn của lực động học do khối lượng mất cân bằng gây ra tại số vòng quay đang tính trên mỗi ổ trục không được vượt quá 200 N, nhưng không lớn hơn 3% giá trị của phản lực trên ổ.
Chú thích – Giá trị giới hạn của khối lượng mặt cân bằng Δm của bánh răng được tính theo công thức:
Δm =
, kg
trong đó:
ΔF – giá trị giới hạn của lực động học do khối lượng mất cân bằng gây ra trên ổ trục đang tính, kG:
W – vận tốc góc, rad/giây;
R – bán kính quay của khối lượng mất cân bằng Δm, m;
l – khoảng cách giữa tâm của các ổ trục, m;
a – khoảng cách từ tâm của trục đang tính đến tâm của bánh răng, m.
1.21. Trong tổ chức sản xuất chuyên môn hóa, những vật liệu dùng để chế tạo những chi tiết chính của hộp giảm tốc (trục, trục răng, bánh răng, vỏ hộp) phải có giấy chứng nhận chất lượng của cơ sở sản xuất vật liệu hoặc giấy thử nghiệm của phòng thí nghiệm của cơ sở chế tạo hộp giảm tốc xác nhận phù hợp với các tiêu chuẩn hiện hành.
1.22. Lượng dư gia công, sai lệch giới hạn của kích thước, của khối lượng, của chiều dầy thành không gia công và của gân đối với vật đúc bằng gang theo cấp chính xác II – TCVN 385-70.
Đối với vật đúc bằng thép, lượng dư gia công và các sai lệch trên theo tài liệu kỹ thuật đã được xét duyệt của cơ sở chế tạo.
1.23. Vật đúc phải làm sạch vẩy và cát của phôi.
1.24. Phôi đúc không được có vết nứt, chai trên bề mặt gia công và các khuyết tật làm xấu hình dạng sản phẩm.
1.25. Ngoài những quy định trong điểm 1.24 những khuyết tật cho phép trên bề mặt có gia công và không gia công của phôi đúc và những phương pháp sửa chữa các khuyết tật không cho phép, được qui định trong điều kiện kỹ thuật của cơ sở chế tạo.
1.26. Khi chế tạo hộp giảm tốc hàng loạt phôi của thân hộp và nắp hộp phải hóa già.
1.27. Vật rèn và dập bằng thép theo tài liệu kỹ thuật của sơ sở chế tạo khi chưa có tiêu chuẩn nhà nước hay tiêu chuẩn ngành.
1.28. Không cho phép sửa chữa bằng hàn vá các phôi rèn và dập.
1.29. Sai lệch giới hạn của các kích thước không chỉ dẫn trên, mặt bao theo A8, mặt bị bao theo B8, các mặt khác bằng ± ½ dung sai cấp 8; sai lệch giới hạn kích thước của các bề mặt không kim loại, mặt bao theo A10, mặt bị bao theo B10.
1.30. Độ không trùng giữa đường viền của thân hộp và nắp hộp theo mặt bích tháo rồi không được vượt quá:
– Đối với hộp giảm tốc dài đến 1000 mm – 2 mm;
– Đối với hộp giảm tốc dài từ 1000 đến 2000 mm – 3 mm;
– Đối với hộp giảm tốc dài trên 2000 – 4 mm.
1.31. Trên các bề mặt có độ nhẵn trong khoảng
4 ÷
6 không được có các vệt cắt, vết lõm và trên bề mặt có độ nhẵn cấp cao hơn ngoài ra không được có vết xước.
1.32. Ren theo quy định của TCVN 2248-77 và TCVN 1917-77.
1.33. Không được phép có vết nứt, vết cháy trên mọi chi tiết của hộp giảm tốc.
1.34. Độ không đồng đều của độ cứng bề mặt vành ngoài và vành trong của bánh răng không được vượt quá 50% dung sai của độ cứng cho trên bản vẽ.
1.35. Tất cả các bề mặt không gia công của những chi tiết đúc bằng gang và bằng thép nằm trong bể dầu của hộp giảm tốc phải sơn sau khi đã sơn lót một lớp sơn chịu dầu hoặc là phải sơn lót hai lần.
1.36. Các trục của hộp giảm tốc đã lắp ráp xong phải quay được bằng tay nhẹ nhàng, êm.
1.37. Đầu của thước chỉ dầu, nút tháo dầu phải sơn màu đỏ.
1.38. Mặt ngoài của hộp giảm tốc phải sơn (trừ tấm nhãn hiệu của nơi chế tạo và các đầu trục nhô ra khỏi hộp).
1.39. Hộp giảm tốc được cung cấp ở dạng lắp, có lý lịch máy bản hướng dẫn sử dụng và lắp ráp kèm theo.
1.40. Hộp giảm tốc phải qua kiểm tra sử dụng ở cơ sở chế tạo. Người chế tạo phải có trách nhiệm trong vòng 2 năm kể từ ngày sử dụng, nhưng không quá ba năm kể từ ngày giao hàng, sửa chữa và thay thế không được tính tiền nếu người sử dụng thực hiện đúng sự hướng dẫn sử dụng.
1.41. Hộp giảm tốc phải sử dụng được đến tải trọng cho phép.
2. NGHIỆM THU
2.1. Hộp giảm tốc phải được kiểm nghiệm bằng thử điển hình hoặc thử nghiệm thu.
2.2. Thử điển hình để xác nhận những số liệu trong lý lịch của hộp giảm tốc và tiến hành khi:
– Chế tạo mẫu mới;
– Cải tiến mẫu chế tạo;
– Sản xuất hàng loạt ổn định thì thử ít nhất một lần trong chu kỳ 3 năm.
2.3. Thử nghiệm điển hình được tiến hành không ít hơn 3 hộp giảm tốc của mỗi cỡ. Khi chế tạo loạt hộp giảm tốc một kiểu, cho phép thử điển hình một số đại diện, nhưng không ít hơn 25% tổng số lượng cỡ trong loạt.
2.4. Thử nghiệm thu phải tiến hành từng hộp giảm tốc để kiểm tra chất lượng chế tạo.
3. PHƯƠNG PHÁP THỬ
3.1. Kiểm tra chất lượng chế tạo hộp giảm tốc phải tiến hành cả hai chiều quay của trục.
3.2. Khi chế tạo hàng loạt, để kiểm tra chất lượng chế tạo hộp giảm tốc bánh răng phải thực hiện:
– Kiểm tra rung động của hộp giảm tốc;
– Kiểm tra vết tiếp xúc.
Kiểm tra rung động là xác định đặc tính rung động của hộp giảm tốc và so sánh với độ rung cho phép.
Phương pháp kiểm tra độ rung được thực hiện theo quy định trong phụ lục của tiêu chuẩn này.
3.3. Khi chế tạo hộp giảm tốc trục vít và chế tạo đơn chiếc hoặc hàng loạt nhỏ hộp giảm tốc bánh răng phải tiến hành:
– Kiểm tra theo phương pháp động học;
– Kiểm tra vết tiếp xúc;
– Kiểm tra nhiệt độ của hộp giảm tốc.
Kiểm tra theo phương pháp động học bao gồm việc xác định các giá trị thành phần của sai số động học của truyền động bánh răng trong hộp giảm tốc và so sánh với các giá trị cho phép.
3.4. Khi chế tạo đơn chiếc cũng như trước khi kiểm tra độ rung và kiểm tra theo phương pháp động học khi chế tạo hàng loạt việc kiểm tra chất lượng chế tạo hộp giảm tốc cho phép tiến hành:
– Kiểm nghiệm độ chính xác của các chi tiết;
– Kiểm nghiệm chất lượng lắp ráp bằng cách chạy rà;
– Kiểm nghiệm đặc tính ồn của hộp giảm tốc.
3.5. Các phương pháp tiến hành thử điển hình và thử nghiệm thu được quy định theo điều kiện kỹ thuật của cơ sở chế tạo.
4. GHI NHÃN, BAO GÓI, VẬN CHUYỂN VÀ BẢO QUẢN
4.1. Trên hộp giảm tốc phải gắn tấm nhãn với nội dung:
– Ký hiệu sản phẩm của cơ sở chế tạo;
– Kiểu hộp giảm tốc và ký hiệu tiêu chuẩn;
– Tỷ số truyền danh nghĩa;
– Mô men xoắn định mức trên trục chậm;
– Khối lượng hộp giảm tốc;
– Số thứ tự theo hệ thống đánh số của cơ sở chế tạo;
– Năm sản xuất.
Chú thích: Trên tấm ghi nhãn cho phép chỉ dẫn số vòng quay định mức.
4.2. Ghi nhãn phải rõ ràng và được bền lâu.
4.3. Việc bao gói phải bảo đảm hộp giảm tốc không bị hư hỏng trong thời gian không ít hơn 3 năm.
4.4. Các đầu trục nằm ngoài hộp giảm tốc phải được bảo vệ để tránh hư hỏng và chống rỉ.
4.5. Then trên các đầu trục và thước chỉ dầu phải được giữ chặt.
4.6. Cách bao gói để vận chuyển do nơi chế tạo chịu trách nhiệm.
4.7. Hộp giảm tốc có thể được vận chuyển bằng phương tiện bất kỳ với điều kiện phải bảo đảm chúng không bị hư hỏng.
4.8. Hộp giảm tốc phải bảo quản trong kho kín, khô ráo.
PHỤ LỤC THAM KHẢO
Phương pháp kiểm tra rung động của hộp giảm tốc
1. Độ rung động của hộp giảm tốc được tiến hành khi quay với tải trọng không thấp hơn 40% tải trọng làm việc và với số vòng quay định mức.
2. Khi đo rung động của hộp giảm tốc phải được lắp đặt sao cho những rung động bên ngoài không ảnh hưởng đến kết quả đo. Với mục đích ấy, không phụ thuộc vào cách lắp đặt khi sử dụng, hộp giảm tốc nhất thiết phải được gá lên nền có giảm chấn.
Cho phép lắp đặt hộp giảm tốc không có giảm chấn, nếu qua kiểm tra xác minh rằng đối với hộp giảm tốc đó khi lắp đặt như thế không làm sai lệch đặc tính rung động.
3. Nếu khi đo đặc tính rung động của hộp giảm tốc phải nối với một cơ cấu hay thiết bị nào khác, nên dùng khớp nối giảm được sự truyền rung động theo trục.
4. Trong trường hộp nối ống, đường dẫn dầu v.v… vào hộp giảm tốc được thử phải nối mềm.
5. Tần số giao động tự do của hộp giảm tốc trên bộ giảm chấn theo hướng vuông góc với mặt tựa của cơ cấu không vượt quá 12 Hz.
6. Độ nhiễu rung động trên ổ trục của hộp giảm tốc được thử phải nhỏ hơn độ rung của hộp giảm tốc làm việc không dưới 10 db so với độ rung nói chung cũng như đối với độ rung trong dải hẹp của tần số.
7. Những đặc tính rung động sau đây phải được xác định:
– Độ rung động chung của hộp giảm tốc trong khoảng tần số từ 20 đến 8000 Hz;
– Độ rung trong những dải hẹp của tần số (không rộng hơn 1/3 bát trình) trong khoảng tần số từ 20 đến 8000 Hz.
8. Rung động phải được đo bằng đề-xi-ben (db) theo trị số hiệu dụng (trung bình của bình phương) của gia tốc.
Ở mức số không giá trị của gia tốc bẳng 3.10-2 cm/s2.
9. Rung động được đo trên ổ trục (trên đế hoặc mặt bích) của hộp giảm tốc theo hướng vuông góc với mặt tựa.
10. Điểm đặt dụng cụ đo rung động trên ổ trục phải chỉ dẫn trên hình vẽ. Đối với một kiểu hộp giảm tốc, vị trí của điểm đó phải thống nhất.
11. Giá trị độ nhiễu chung và độ nhiễu trong dải hẹp của tần số được đo cũng tại điểm đo rung động. Tiến hành đo khi đã lắp vào và cho hoạt động tất cả các cơ cấu phụ bảo đảm sự làm việc bình thường của hộp giảm tốc được thử.
12. Mức rung của hộp giảm tốc do cơ sở chế tạo quy định đối với mỗi kiểu cỡ hộp giảm tốc và phải được cấp quản lý duyệt:
– Khi chế tạo theo mẫu mới;
– Khi kết cấu hoặc công nghệ chế tạo hộp giảm tốc có thay đổi có thể làm ảnh hưởng đến đặc tính rung động;
– Kiểm tra định kỳ không ít hơn một lần trong 3 năm.
13. Mức rung được quy định qua thử nghiệm 10 hộp giảm tốc cùng 1 kiểu cỡ, độ chính xác chế tạo của các hộp giảm tốc này phải phù hợp với những yêu cầu trong các tài liệu kỹ thuật.
Từ 10 hộp giảm tốc này chọn được các mẫu thử độ rung động chung của các mẫu thử không được vượt quá độ rung chung của cái tốt nhất trong đó lớn hơn 4 db, còn độ rung trong dải tương ứng của tần số (không rộng hơn 1 bát trình) không vượt quá độ rung tối thiểu trong dải tương ứng lớn hơn 5 db.
14. Giá trị độ rung chung của hộp giảm tốc kém nhất trong các mẫu thử được nói trong điều 13 của phụ lục này được gọi là mực của độ rung chung.
Độ rung lớn nhất trong dải tương ứng của tần số của các hộp giảm tốc đã nói trong điều 13 của phụ lục này được gọi là mực độ rung đối với mỗi dải của tần số (không rộng hơn 1/3 bát trình).
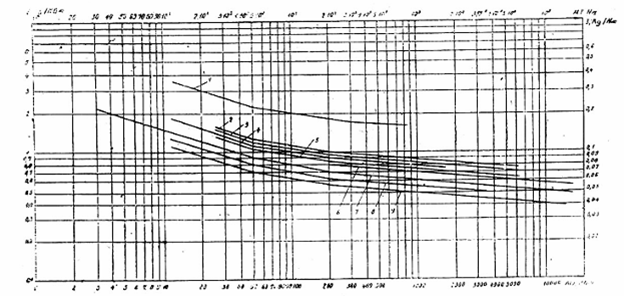
1. Hộp giảm tốc bánh răng côn (u = 1 ÷ 2,8); 2. Hộp giảm tốc bánh răng côn – Trụ ba bậc; 3. Hộp giảm tốc bánh răng côn – trụ hai bậc, hộp giảm tốc trục vít – bánh răng trụ hai bậc; 4. Hộp giảm tốc bánh răng côn (u = 3,15 ÷ 5), hộp giảm tốc trục vít không vạn năng [MT ≥ 1000 Nm (100 KGm)]; 5. Hộp giảm tốc bánh răng trụ hai bậc dạng không đối xứng; 6. Hộp giảm tốc bánh răng trụ ba bậc; 7. Hộp giảm tốc bánh răng trụ hai bậc dạng đối xứng, Hộp giảm tốc bánh răng trụ hai bậc đồng trục, hộp giảm tốc hành tinh hai bậc, hộp giảm tốc trục vít vạn năng không có bộ phận làm nguội [MT ≤ 2000 Nm (200KGm)]; 8. Hộp giảm tốc hành tinh một bậc (i = 3,15 ÷ 12,5), hộp giảm tốc hành tinh một bậc (u = 50 ÷ 10000); 9. Hộp giảm tốc bánh răng trụ một bậc.