TIÊU CHUẨN NHÀ NƯỚC
TCVN 1835 – 76
ĐUI ĐÈN
Tiêu chuẩn này áp dụng cho các loại đui đèn điện thường dùng (sau gọi tắt là đui đèn), để đưa nguồn điện tới các bóng đèn thắp sáng bằng dây tóc thông thường.
1. PHÂN LOẠI
1.1. Đui đèn được phân loại theo các kiểu sau:
a) Phân loại theo cách lắp với bóng đèn:
– kiểu xoáy ốc (vặn)
– kiểu ngạnh.
b) Phân loại theo cách lắp đặt:
– kiểu treo
– kiểu mặt bích
– kiểu nối ống.
c) Phân loại theo dạng bảo vệ:
– kiểu thông thường
– kiểu chống mưa.
d) Phân loại theo nguyên liệu dùng làm vỏ:
– loại có vỏ cách điện
– loại có vỏ kim loại.
e) Phân loại theo mức độ an toàn:
– kiểu an toàn
– kiểu nửa an toàn
g) Phân loại theo dạng có lắp công tắc hay không:
– kiểu có công tắc
– kiểu thông thường (không có công tắc).
Chú thích. Kiểu chống mưa không được lắp công tắc đi kèm.
1.2. Các thông số cơ bản của đui đèn phải phù hợp với quy định trong bảng 1.
Bảng 1
Kiểu
|
Ký hiệu
|
Điện áp làm việc cao nhất (V)
|
Dòng điện làm việc lớn nhất (A)
|
Công suất lớn nhất của bóng đèn cần lắp (W)
|
Đui xoáy
|
E10
|
50
|
2,5
|
25
|
E14
|
250
|
60
|
E27
|
4
|
300
|
E40
|
10
|
1 000
|
20
|
2 000
|
Đui ngạnh
|
1B9
|
50
|
2,5
|
25
|
1B15
|
250
|
2,5*
|
40
|
1B15A
|
2B15
|
2B15A
|
2B22
|
4
|
300
|
* Nếu cần, cho phép chế tạo kiểu đui đèn có dòng điện làm việc lớn nhất là 4A.
Chú thích:
1. Chữ E là đui xoáy, số sau chữ E chỉ đường kính ngoài ren xoáy ốc của đui đèn đã quy tròn.
2. Chữ B là đui ngạnh, số đứng trước chữ B chỉ số cọc lò xo tiếp xúc của đui đèn, số sau chữ B chỉ đường kính trong của cổ đui ngạnh, chữ cuối – A là loại đui ngạch mà rãnh ở hai bên có chiều cao so le nhau.
3. Tích số của điện áp làm việc cao nhất với dòng điện làm việc lớn nhất ghi trên bảng 1 không đặc trưng cho công suất lớn nhất mà đui đèn có thể chịu đựng được. Ba thông số ghi trong bảng là ba chỉ tiêu độc lập để giới hạn phạm vi sử dụng của đui đèn.
1.3. Kích thước ren của đui xoáy phải phù hợp với quy định trong bảng 2 theo hình 1.
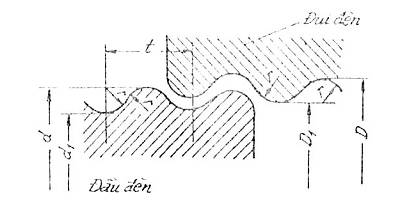
Hình 1
bảng 2
Ký hiệu
|
t
|
r
|
D
|
D1
|
Nhỏ nhất
|
Lớn nhất
|
Nhỏ nhất
|
Lớn nhất
|
E10
|
1,814
|
0,531
|
9,61
|
9,78
|
8,59
|
8,76
|
E14
|
2,822
|
0,822
|
13,97
|
14,16
|
12,37
|
12,56
|
E27
|
3,629
|
1,025
|
26,55
|
26,85
|
24,36
|
24,66
|
E40
|
6,350
|
1,850
|
39,60
|
40,05
|
36,00
|
36,45
|
1.4. Sau khi lắp bóng đèn tương ứng vào đui xoáy, khoảng cách tương đối giữa phần ren và tấm tiếp xúc phải phù hợp với quy định ghi trong bảng 3 và hình 2
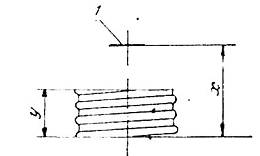
|
Hình 2
1. Vị trí là tiếp xúc của đui xoáy sau khi lắp bóng đèn.
|
Bảng 3
Ký hiệu
|
X
|
Y
|
Nhỏ nhất
|
Lớn nhất
|
Nhỏ nhất
|
E10
|
7,5
|
9,3
|
–
|
E14
|
12
|
15
|
5
|
E27
|
17
|
21
|
7
|
E40
|
27
|
32
|
12
|
1.5. Kích thước cơ bản của đui ngạnh phải phù hợp với quy định trong bảng 4 và hình 3.
mm Bảng 4
Ký hiệu kích thước
|
1 B9
|
1 B15
|
1 B15A
|
2 B15
|
2 B15A
|
2 B22
|
A
|
Nhỏ nhất
|
2,2
|
2,7
|
2,7
|
2,7
|
2,7
|
2,7
|
Lớn nhất
|
2,4
|
3,2
|
3,2
|
3,2
|
3,2
|
3,2
|
B
|
Nhỏ nhất
|
0,7
|
0,8
|
0,8
|
0,8
|
0,8
|
0,9
|
Lớn nhất
|
0,9
|
1,0
|
1,0
|
1,0
|
1,0
|
1,2
|
C
|
Nhỏ nhất
|
9,35
|
15,3
|
15,3
|
15,3
|
15,3
|
22,2
|
Lớn nhất
|
9,45
|
15,5
|
15,5
|
15,5
|
15,5
|
22,5
|
D
|
Lớn nhất
|
3,5
|
5,0
|
7,0
|
5,0
|
7,0
|
5,0
|
E
|
Lớn nhất
|
4,0
|
4,9
|
4,9
|
4,9
|
4,9
|
4,9
|
F
|
Nhỏ nhất
|
7,6
|
9,0
|
9,0
|
9,0
|
9,0
|
10,0
|
G
|
Nhỏ nhất
|
–
|
–
|
–
|
7,9
|
7,9
|
10,5
|
Lớn nhất
|
–
|
–
|
–
|
9,7
|
9,7
|
13,2
|
H
|
Khoảng
|
0,95
|

|

|

|

|

|
I
|
Nhỏ nhất
|
2,7
|
2,7
|
2,7
|
2,7
|
2,7
|
3,5
|
Lớn nhất
|
5,0
|
5,0
|
5,0
|
3,0
|
3,0
|
4,0
|
J
|
Nhỏ nhất
|
0,45
|
0,45
|
0,45
|
0,45
|
0,45
|
0,45
|
K
|
Nhỏ nhất
|
–
|
1,3
|
1,3
|
1,3
|
1,3
|
1,5
|
L
|
Lớn nhất
|
–
|
21
|
21
|
21
|
21
|
28
|
M
|
Nhỏ nhất
|
–
|
–
|
3,4
|
–
|
3,4
|
–
|
Lớn nhất
|
–
|
–
|
3,6
|
–
|
3,6
|
–
|
a
|
Khoảng
|
37o
|
29o
|
29o
|
29o
|
29o
|
23o
|
b
|
Nhỏ nhất
|
–
|
–
|
–
|
82o30’
|
82o30’
|
82o30’
|
Lớn nhất
|
–
|
–
|
–
|
97o30’
|
97o30’
|
97o30’
|
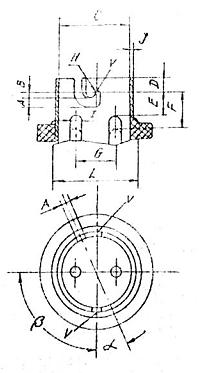
|
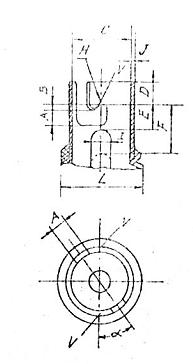
|
Hình 3a. Đui đèn cổ kim loại có hai cọc tiếp xúc
|
Hình 3b. Đui đèn cổ kim loại có một cọc tiếp xúc
|
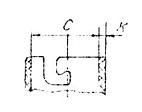
|
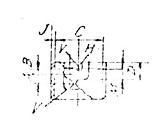
|
Hình 3c. Đui đèn cổ nhựa
|
Hình 3d. Đui đèn có hai rãnh so le
|
Chú thích. V – điểm định vị của ngạnh bóng đèn
F – kích thước cực hạn của cọc tiếp xúc khi bị nén.
2. YÊU CẦU KỸ THUẬT
2.1. Đui đèn phải phù hợp với các yêu cầu trong tiêu chuẩn này và các tài liệu kỹ thuật khác đã được phê chuẩn.
2.2. Đui đèn phải làm việc được ở các điều kiện sau:
a) Độ cao so với mặt biển không quá 1 000 m.
b) Nhiệt độ của môi trường xung quanh không quá + 40oC.
c) Độ ẩm tương đối của môi trường xung quanh không quá 98% (ở nhiệt độ 25oC)
d) Không có chất khí cháy, nổ, ăn mòn kim loại hoặc phá hoại chất cách điện; không có bụi dẫn điện.
e) Có phương tiện che mưa.
Chú thích. Điều (c) không áp dụng cho đui đèn kiểu chống mưa.
2.3. Cách điện của đui đèn phải chịu được thử điện áp xoay chiều 2000 V tần số 50 Hz trong một phút mà không bị đánh thủng hoặc phóng điện bề mặt.
2.4. Đui đèn kiểu chống mưa phải thử mưa nhân tạo với lượng mưa mỗi phút 3 mm, xiên góc 15o so với đường thẳng đứng. Sau 30 phút thử, nước mưa không được lọt vào trong và phải chịu được thử điện áp xoay chiều 1 500 V tần số 50 Hz trong một phút mà không bị đánh thủng hoặc phóng điện bề mặt.
2.5. Đui đèn phải chịu được thử khí hậu nhân tạo theo TCVN 1612 – 75, thời gian thử là 21 chu kỳ. Sau khi thử tính năng cách điện của đui đèn phải đạt các yêu cầu sau:
a) Điện trở cách điện không nhỏ hơn 2 MW.
b) chịu được thử điện áp xoay chiều 1 500 V tần số 50 Hz trong một phút mà không bị đánh thủng hoặc phóng điện bề mặt.
2.6. Cấu tạo của đui vặn phải đạt các yêu cầu sau:
a) Đui xoáy E14 và E27 kiểu an toàn đem lắp với bóng đèn tương ứng, từ khi bắt đầu vặn bóng vào tới khi vặn xong, tay không tiếp xúc tới bộ phận mang điện của bóng đèn và đui xoáy.
b) Đui xoáy E11 và E27 kiểu nửa an toàn, sau khi vặn xong bóng đèn tương ứng vào rồi thì tay không tiếp xúc tới bộ phận mang điện của bóng đèn và đui xoáy.
c) Đui xoáy E40 sau khi vặn xong bóng đèn tương ứng vào rồi thì tay không tiếp xúc tới bộ phận mang điện của bóng đèn và đui xoáy.
2.7. Với kiểu đui đèn có công tắc, sau khi cách điện của núm công tắc bị bong ra, tay vẫn không tiếp xúc tới chi tiết mang điện của đui đèn.
2.8. Khi cọc lò xo tiếp xúc của đui ngạnh bị nén tới vị trí làm việc bình thường thì tổng lực đẩy của chúng phải phù hợp với quy định trong bảng 5.
Bảng 5
Ký hiệu
|
Tổng lực đẩy (N)
|
2 B15
|
10 ¸ 20
|
2 B22
|
15 ¸ 25
|
2.9. Cho đui đèn làm việc với 125% dòng điện làm việc lớn nhất, độ tăng nhiệt của các bộ phận mang điện không được quá 30oC
2.10. Đui đèn phải chịu được thử thao tác 500 lần với phụ tải thuần điện trở theo quy định trong bảng 6. Với loại đui đèn có công tắc thì công tắc còn phải thử “bật tắt” được 10 000 lần phụ tải thuần điện trở theo quy định trong bảng 6.
Bảng 6
Ký hiệu
|
Điện áp thử (V)
|
Dòng điện thử (A)
|
E 14, 2 B15
|
250
|
2,5*
|
E 27, 2 B22
|
250
|
4
|
E 40
|
không có phụ tải
|
* Chú thích. Với đui đèn 2 B15 nếu chế tạo với dòng điện 4A thì dòng điện thử là 4 A.
Sau khi thử, đui đèn phải đạt các yêu cầu sau:
a) Các chi tiết của đui đèn không bị hư hỏng làm ảnh hưởng tới sự làm việc bình thường của đui đèn, ví dụ: các chi tiết lắp xiết bị long ra, lò xo không đàn hồi, cách điện bị vỡ v.v…
b) Chịu được thử điện áp xoay chiều 1 500 V tần số 50 Hz trong một phút mà không bị đánh thủng hoặc phóng điện bề mặt.
c) Cho làm việc với dòng điện làm việc lớn nhất mà độ tăng nhiệt của các bộ phận mang điện không quá 40 oC.
2.11. Đui đèn phải có độ bền cơ học, cụ thể là:
a) Vỏ cách điện của đui đèn phải chịu được thử va đập 5 lần với độ cao 100mm vẫn không bị rạn nứt mà mắt nhìn thấy được.
Búa thử làm bằng gỗ cứng có khối lượng 0,15 kg, búa hình bán cầu có bán kính 10 mm. Cán búa bằng thép ống dày 0,5 mm, đường kính ngoài là 9 mm, chiều dài tác dụng của cán búa là 1m.
Độ cao thử va đập là khoảng cách của hình chiếu đứng từ điểm tiếp xúc trên mặt búa tới điểm bị va đập trên mẫu thử (xem hình 10).
b) Đui vặn phải chịu được thử mômen xoắn theo quy định ở bảng 7 trong 1 phút mà không bị nứt vỡ, các chi tiết lắp xiết không bị lỏng, và không có các hiện tượng hư hỏng khác làm ảnh hưởng tới sự làm việc bình thường của đui đèn.
Bảng 7
Ký hiệu
|
Mômen xoắn (N.cm)
|
E 14
|
100
|
E 27
|
180
|
E 40
|
300
|
2.12. Đui đèn phải chịu được thử nóng với nhiệt độ như bảng 8 trong thời gian 16 giờ mà không bị hư hỏng làm ảnh hưởng tới sự làm việc bình thường của đui đèn như lò xo không đàn hồi, cách điện bị nứt vỡ phồng rộp hoặc chảy ra v.v…
Bảng 8
Ký hiệu
|
Nhiệt độ thử (oC)
|
E 14, 2 B15
|
130
|
E 27, 2 B22
|
180
|
E 40
|
220
|
Với các chi tiết bịt kín và dây dẫn ra của đui đèn kiểu chống mưa thì nhiệt độ thử là 100oC thời gian là 16 giờ. Sau khi thử các chi tiết đó không được rạn nứt.
Sau khi thử chịu nóng, kích thước lắp ghép của đui đèn phải đạt các yêu cầu sau:
a) Với đui ngạnh dùng dưỡng kiểm, hình 13 phần phụ lục, đút lọt vào đui đèn.
b) Với đai xoáy dùng dưỡng kiểm, hình 12 phần phụ lục, vặn được vào đui xoáy.
2.13. Vỏ đui đèn kiểu chống mưa phải chịu được thử lạnh đột ngột giảm 90oC mà không bị biến dạng, nứt vỡ.
2.14 Các chi tiết của đui đèn bằng kim loại đen phải có một lớp bảo vệ chống gỉ, lớp bảo vệ đó phải phù hợp với các yêu cầu sau:
a) Lớp bảo vệ không được có hiện tượng bong tróc, rỗ rộp hoặc cục bộ có chỗ không có lớp bảo vệ.
b) Sau 48 giờ thử sương muối, trên mặt lớp bảo vệ không được xuất hiện vết gỉ nâu và tổng diện tích lớp gỉ trắng không được quá 3%.
Các điều kiện thử sương muối:
– Thành phần nước muối:
Natri clorua 27 g/l
Magie clorua 6 g/l
Canxi clorua 1 g/l
Kali clorua 1g/l
Độ pH 6,5 ¸ 7,2
– Nhiệt độ thử 35 ± 20C
– Độ ẩm tương đối 90% trở lên
– Chu kỳ phun sương: cứ cách 45 phút lại phun liền trong 15 phút. Theo chu kỳ đó phun đủ thời gian quy định ở trên.
– Mật độ hạt sương: 5 x 105 ¸ 10 x 106 hạt/cm3.
– Đường kính hạt sương 1 ¸ 5 mm chiếm 85% trở lên.
2.15 Các chi tiết của đui đèn làm bằng đồng hoặc hợp kim đồng đem ngâm trong dung dịch 10 g nitrat thủy ngân và 10 ml axit nitric (tỉ trọng 1,42); sau 30 phút các chi tiết vẫn không bị rạn nứt.
2.16 Bề mặt các chi tiết cách điện của đui đèn phải đạt yêu cầu sau:
a) Bề mặt các chi tiết bằng nhựa phải láng bóng không được phồng rộp, rỗ, rạn nứt, sắc cạnh.
b) Các chi tiết bằng sứ phải phù hợp các quy định về sứ cách điện.
2.17 Cọc nối dây của đui đèn kiểu mặt bích phải nối được 1 và 2 dây dẫn có mặt cắt như quy định trong bảng 9. Các loại đui đèn khác thì có thể nối được 1 dây dẫn có mặt cắt như quy định trong bảng 9.
2.18 Nối dây dẫn có mặt cắt như quy định trong bảng 9 tới cọc nối dây của đui đèn rồi cho thử kéo 100 lần, mỗi lần chịu lực kéo là 25 N trong một giây. Sau khi thử số sợi bị kéo đứt không được quá 1/3 tổng số sợi có trong dây dẫn, độ xê dịch của dây dẫn không được lớn hơn 2mm.
Bảng 9
Ký hiệu
|
Mặt cắt của một dây dẫn (mm2)
|
E14, 2B15
|
0,5 ¸ 1
|
E27, 2B22
|
0,5 ¸ 2,5
|
E40
|
1 ¸ 4
|
2.19 Nếu trên đui đèn kiểu chống mưa có lắp sẵn dây dẫn cố định không tháo ra được thì dây đó phải là loại dây dùng ngoài trời có nhiều sợi mềm và có mặt cắt theo đúng quy định trong bảng 9. Chiều dài dây dẫn không được ngắn hơn 150 mm.
2.20 Phần ren của đui đèn phải đạt các yêu cầu sau:
a) Phần ren nối ghép giữa kim loại với nhau phải có số vòng nối hữu ích không ít hơn 2 vòng.
b) Phần ren nối ghép giữa nhựa cách điện với nhau phải có số vòng hữu ích không ít hơn 2,5 vòng.
2.21 Đui xoáy kiểu E27 nếu có bộ phận để lắp chụp đèn thì đường kính ngoài phần ren trên vỏ đui xoáy không được lớn hơn 33,7 mm và có bước ren bằng 1,25 mm.
2.22. Đui đèn kiểu có công tắc, ngoài tiêu chuẩn này ra, phần công tắc còn phải phù hợp tiêu chuẩn TCVN 1834-76 về “công tắc”.
3. PHƯƠNG PHÁP THỬ
3.1 Kiểm tra kích thước lắp ghép của đui đèn với bóng đèn (điều 1.3, 1.4, 1.5), dùng các dưỡng kiểm ở phần phụ lục.
a) Với đui xoáy dùng dưỡng kiểm như hình 12 và kích thước theo bảng 12 và 13 phần phụ lục. Khi kiểm, đầu dưỡng có ren phải vặn trơn nhẹ vào đui đèn, còn đầu kia do sức nặng của bản thân dưỡng trơn sẽ không lọt vào được.
b) Với đui ngạnh dùng dưỡng kiểm như hình 13 và kích thước theo bảng 14 phần phụ lục. Khi kiểm, đầu dưỡng có ngạnh phải lọt vào đui đèn một cách nhẹ nhàng, còn đầu kia do sức nặng của bản thân dưỡng trơn sẽ không lọt vào được.
3.2. Kiểm tra các kích thước, vật liệu và mặt ngoài của đui đèn (2.14a, 2.16, 2.19, 2.20, 2.21 và 4.1) có thể quan sát bằng mắt, kết hợp với các dụng cụ đo kiểm cần thiết khác.
3.3. Thử chịu điện áp (điều 2.3)
Thử trong điều kiện làm việc bình thường. Tiến hành thử chịu điện áp giữa các cọc tiếp xúc với nhau và giữa các cọc đã nối liền lại với vỏ. Vỏ cách điện của đui đèn được bọc bằng một lớp giấy kim loại và nối với một cực điện để thử.
Với kiểu đui đèn có công tắc thì phải thử ở vị trí công tắc “tắt và bật”. Núm công tắc phải bọc giấy kim loại và nối liền với giấy kim loại đã bọc ngoài vỏ đui đèn.
Dung lượng của máy biến áp thử không nhỏ hơn 0,5 KVA.
3.4. Thử chống mưa (điều 2.4)
Thử trong thiết bị chuyên dùng có vòi phun mưa nhân tạo. Khi thử phải điều chỉnh lượng mưa theo quy định của tiêu chuẩn này. Lượng mưa đo bằng “cốc đo mưa” hoặc cốc đựng khác để vào vị trí thử sau một thời gian rồi lấy ra tính theo công thức:
Lượng mưa =
(mm/ph)
trong đó:
P – khối lượng nước mưa đo được (g)
S – mặt cắt miệng cốc đo (cm3)
t – thời gian đo (ph)
Lắp bóng vào đui đèn rồi treo vào thiết bị thử, phun đều, liên tục mưa nhân tạo xiên góc 45o so với trục treo đèn. Sau 30 phút lấy mẫu ra tháo bóng ra khỏi đui đèn rồi kiểm tra theo thứ tự sau:
a) Thử chịu điện áp theo điều 3.3.
b) Kiểm tra bằng mắt xem nước có lọt vào chỗ cọc nối dây và các bộ phận gần đó không. Việc kiểm tra phải làm xong trong vòng 20 phút kể từ lúc ngừng mưa nhân tạo.
3.5. Thử khí hậu nhân tạo (điều 2.5)
Treo đui đèn vào tủ (buồng) với các điều kiện phù hợp với quy định trong điều 2.5. Nếu nhiệt độ đui đèn chênh lệch nhiều so với nhiệt độ của tủ (buồng) thì phải để đui đèn ở môi trường có nhiệt độ như nhiệt độ của tủ (buồng) ít nhất là 4 giờ.
Sau 21 chu kỳ thử thì thử tính năng cách điện bằng cách thực hiện ngay trong tủ theo thứ tự sau:
a) Đo điện trở cách điện bằng mêgôm kế 500 V.
b) Thử chịu điện áp như điều 2.5b.
3.6. Thử chống điện giật (điều 2.6)
Lắp bóng đèn tương ứng vào đui đèn như quy định trong điều 2.6. Dùng que thử như hình 4 và lắp sơ đồ theo hình 5. Điện áp thử không quá 40 V.
Với đui đèn kiểu an toàn E14 và E27 để que thử tiếp xúc tới phần ren của bóng đèn, trong suốt quá trình vặn bóng đèn vào đui mà đèn tín hiệu không sáng thì coi là thử đạt yêu cầu.
Với đui đèn xoáy E 40 và kiểu nửa an toàn E14 và E27 thì sau khi lắp bóng đèn vào rồi, cố để que thử tiếp xúc tới phần ren của đui và bóng đèn mà đèn tín hiệu không sáng là đạt yêu cầu.
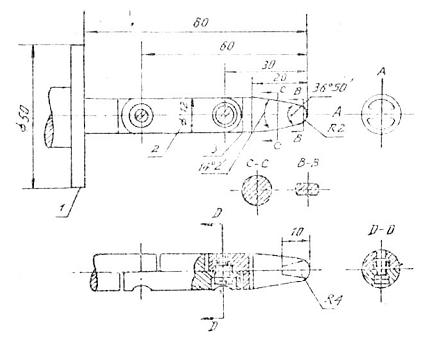
Hình 4
1. Làm bằng chất cách điện. 2 và 3. Bằng kim loại
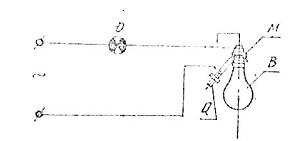
Hình 5
|
Đ. Đèn tín hiệu
|
B. Đèn thử
|
M. Mẫu thử
|
Q. Que thử
|
3.7 Kiểm tra núm công tắc (điều 2.7)
Bỏ đi phần cách điện của núm công tắc chìa ra ngoài đui đèn, rồi thử theo hình 6, cho que thử vào phần chìa ra đó nếu tín hiệu không sáng được coi là đạt yêu cầu.
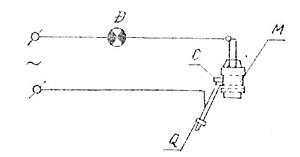
Hình 6
|
Đ. Đèn tín hiệu
|
C. Núm công tắc sau khi đã bóc lớp cách điện ngoài
|
M. Mẫu thử
|
Q. Que thử
|
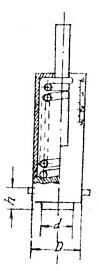
|
3.8. Đo lực đàn hồi của cọc lò xo (điều 2.8)
Đo bằng lực kế như hình 7 và theo các trị số quy định trong bảng 10.
Giữ đui đèn cố định rồi lắp hẳn lực kế vào đui đèn. Đẩy từ từ cán của lực kế cho tới khi hai ngạnh của lực kế vừa rời khỏi điểm định vị của rãnh hãm trên đui đèn, thì đọc số chỉ trên lực kế. Chú ý khi đẩy cán lực kế luôn giữ cho đường trục của lực kế trùng với đường trục của đui đèn.
Đo 5 lần và lấy số chỉ giống nhau trong 3 lần đo trở lên làm trị số đo, hoặc lấy trị số trung bình của 5 lần đo làm trị số đo
|
Hình 7
|
mm Bảng 10
Ký hiệu
|
D
|
d
|
h
|
2 B15
|
F 15 ± 0,2
|
F 12
|
7 ± 0,1
|
2 B22
|
F 21,75 ± 0,3
|
F 18
|
7,5 ± 0,1
|
3.9. Thử độ tăng nhiệt độ (điều 2.9)
Thử trong buồng thử không có ảnh hưởng của luồng gió, tia nắng và các bức xạ nhiệt khác. Sơ đồ thử mắc theo hình 8. Dây dẫn nối mạch điện dùng loại dây có mặt cắt lớn nhất theo quy định trong bảng 9.
Điều chỉnh dòng điện đến trị số quy định đi qua đui đèn. Nhiệt độ tăng đạt tới trị số ổn định khi mà nhiệt độ thay đổi chỉ có 1oC trong vòng 30 phút. Lấy nhiệt độ cao nhất đã ổn định trừ đi nhiệt độ trong phòng được độ tăng nhiệt.
Cố gắng gắn nhiệt kế nhiệt ngẫu vào gần chỗ tiếp xúc của đui đèn nhưng không được làm ảnh hưởng tới sự tiếp xúc giữa đui đèn với bóng đèn.
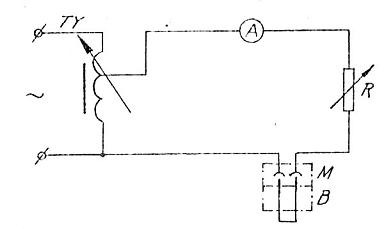
Hình 8
|
TY. Biến áp tự ngẫu
|
A. Ampe kế xoay chiều
|
R. Biến trở
|
M. Mẫu thử
|
B. Bóng đèn
|
|
3.10. Thử thao tác (điều 2.10)
Thử trên thiết bị chuyên dùng mắc theo sơ đồ hình 9. Kẹp chặt đui đèn trên giá, dùng bóng đèn tương ứng làm phụ tải theo quy định ở bảng 6. Đóng và cắt mạch điện thử bằng cách lắp và tháo bóng đèn khoảng 15 lần trong một phút.
Với đui ngạnh, cho ngạnh của bóng đèn lọt vào rãnh hình chữ L của đui đèn, quay một góc cho ngạnh nằm vào vị trí làm việc bình thường, sau đó quay ngược trở lại lùi bóng đèn ra.
Với đui xoáy thì vặn vào vặn ra bóng đèn với tốc độ quay 60 vòng/phút, khi vặn bóng đèn vào thì vặn với mômen xoắn như quy định trong bảng 11.
Bảng 11
Ký hiệu
|
Mômen, N.cm
|
E 14
|
80
|
E 27
|
120
|
E 40
|
250
|
Sau khi thử lau sạch bụi và các vết bẩn trên đui đèn rồi kiểm tra bằng mắt các chỗ xem có hư hỏng không.
Tiếp đó thử chịu điện áp theo điều 3.3 và thử độ tăng nhiệt theo điều 3.9.
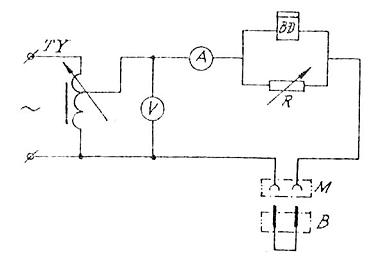
Hình 9
|
TY. Biến áp tự ngẫu
|
V. Von kế xoay chiều
|
A. Ampe kế xoay chiều
|
R. Biến trở
|
M. Mẫu thử B. Bóng đèn
|
BĐ. Bộ đếm
|
|
|
|
3.11. Thử độ bền cơ học (điều 2.11)
a) Thử độ bền cơ học của vỏ đui đèn (điều 2.11a) theo sơ đồ ở hình 10.
Lắp thiết bị thử lên tường, kẹp chặt mẫu thử lên tấm đế sao cho điểm chịu lực trùng với đỉnh búa (khi búa thẳng đứng) và khi búa tiếp xúc với mẫu thử thì mặt phẳng tiếp xúc phải vuông góc với đường trục của búa.
Điều chỉnh chiều cao va đập theo quy định rồi dùng chốt hãm lại, khi rút chốt thì búa sẽ rơi tự do và đập vào mẫu thử.
Các điểm chịu lực ở 5 điểm như sau:
– Với đui ngạnh: 3 điểm trên vỏ cách điện ở chỗ mỏng nhất, 2 điểm ở hai bên cổ đui đèn chỗ đường vuông góc với trục nối giữa hai rãnh chữ L.
– Với đui xoáy: phân bố ở các chỗ mỏng nhất trên vỏ đui đèn.
b) Thử độ bền cơ học của phần ren đui xoáy (điều 2.11b) bằng thiết bị chuyên dùng. Theo quy định về mômen xoắn trong bảng 7, vặn bóng đèn tương ứng vào hết rồi giữ lại chừng 1 phút, lại vặn ngược trở ra rồi kiểm tra bằng mắt.
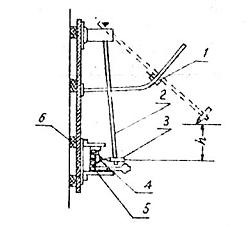
Hình 10
|
1. Chốt định vị
|
2. Cán búa;
|
3. Búa;
|
4. Mẫu thử;
|
5. Tấm đế (bakêlit dày 8 mm diện tích 175 x 175 mm),
|
6. Giá đỡ
|
h. Chiều cao va đập
|
3.12. Thử chịu nóng (điều 2.12)
Cho đui đèn vào tủ, trong khoảng thời gian 30 – 60 phút, đốt nóng cho nhiệt độ trong tủ tăng đạt trị số quy định trong bảng 8 giữa nhiệt độ liên tục 16 giờ. Trong thời gian giữ nhiệt, độ sai lệch của nhiệt độ trong tủ không được quá ± 5oC. Sau thời gian quy định thì mở tủ để cho mẫu thử nguội tự nhiên tới nhiệt độ trong phòng. Lấy mẫu ra và kiểm tra bằng mắt.
Với đui đèn kiểu chống mưa thì đem phần dây dẫn ra của đui đèn quấn lên một trục kim loại có đường kính F 20, sau khi thử xem lớp dây dẫn có bị nứt rạn không.
Cuối cùng dùng dưỡng kiểm như điều 3.1 để kiểm tra kích thước lắp ghép của đui đèn.
3.13. Thử lạnh đột ngột (điều 2.13)
Cho đui đèn kiểu chống mưa vào tủ sấy rồi tăng nhiệt độ của tủ sấy cho tới khi có nhiệt độ cao hơn nhiệt độ của nước làm lạnh 90oC. Sau 2 giờ lấy đui đèn ra và lập tức ngâm vào nước làm lạnh, sau 3 phút thì kiểm tra bằng mắt.
Lượng nước dùng làm lạnh phải đủ để cho sự thay đổi về nhiệt độ trước và sau khi thử chênh lệch không quá 2oC.
3.14. Thử sương muối lớp bảo vệ các chi tiết bằng kim loại đen (điều 2.14)
Rửa sạch dầu mỡ bám trên các chi tiết rồi để vào tủ (buồng) thử có các điều kiện như quy định trong điều 2.14. Trong suốt thời gian thử (48 giờ) sương muối không được ngưng đọng thành giọt trên mặt vật thử, sau đó lấy mẫu ra rửa sạch bằng nước rồi kiểm tra vết gỉ.
3.15. Thử chống rạn nứt (điều 2.15)
Pha chế dung dịch thử như sau: đem 10 ml axit nitric (tỷ trọng 1,42) pha với 30 ml nước cất, lại lấy 11,4 g nitrat thủy ngân ngậm 2 phân tử nước (HgNO3.2H2O) hoặc 10,7 g nitrat thủy ngân ngậm 1 phân tử nước (HgNO3.H2O) hòa tan vào dung dịch trên. Sau khi hòa tan hết, pha thêm nước cất cho đủ 1000 ml.
Lượng dung dịch để thử lấy theo bề mặt của vật thử với tỷ lệ 1 ml/1 cm2.
Sau khi rửa sạch dầu mỡ và lau khô rồi đem mẫu thử ngâm vào dung dịch kể trên, sau 30 phút lấy ra rửa sạch bằng nước rồi lau khô và kiểm tra bề mặt mẫu thử bằng mắt.
Chú thích. Nitrat thủy ngân rất độc nên trong khi pha chế và thử phải đeo khẩu trang và găng tay.
3.16. Kiểm tra khả năng nối dây (2.17)
Lần lượt nối một đoạn dây (với đui đèn kiểu mặt bích thì nối 2 dây) có mặt cắt lớn nhất và nhỏ nhất theo quy định trong bảng 9 tới cọc nối dây. Nếu dây có mặt cắt nhỏ hơn 1 mm2 thì dùng dây mềm, mặt cắt lớn hơn 1 mm2 thì dùng dây cứng. Khi thử thì xiết chặt rồi nới lỏng 5 lần vít giữ dây, sau mỗi lần xiết chặt thì lại kiểm tra xem dây dẫn có bị bong tuột ra khỏi cọc không.
3.17. Kiểm tra sức chịu kéo của đui đèn treo (điều 2.18)
Nối đui đèn với dây dẫn nhiều ruột mềm theo quy định trong bảng 9. Bắt chặt vít vào một đầu dây, còn đầu dây tự do đem treo vật nặng có khối lượng bằng 2,5 kg. Lắp mẫu thử lên thanh ngang của thiết bị thử chuyên dùng như hình 11, cho bánh xe lệch tâm quay với tốc độ 1 vòng/s. Khi bánh xe lệch tâm quay xuống thấp, vật nặng rơi trên mặt đỡ và lực kéo không tác dụng lên mẫu thử; khi bánh xe lệch tâm quay lên cao, tay đòn nâng mẫu thử lên và vật nặng cũng bị nâng lên khỏi mặt đỡ làm cho lực kéo tác dụng lên mẫu thử.
Sau 100 lần thử kéo thì lấy mẫu thử ra đo độ xê dịch của dây dẫn và đếm số sợi dây bị đứt.
Trước khi thử vạch sẵn một vạch dấu trên dây dẫn về phía gần sát chỗ ra dây của đui đèn, đo khoảng cách từ chỗ vạch dấu đến chỗ ra dây của đui đèn hai lần trước và sau khi thử. Độ xê dịch của dây dẫn là hiệu số của hai lần đo kể trên.
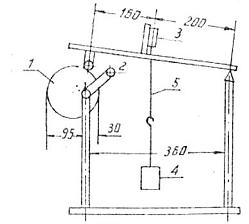
Hình 11
|
1. Bánh lệch tâm
|
2. Tay quay
|
3. Mẫu thử
|
4. Vật nặng
|
3.18. Các đui đèn phải kiểm tra phù hợp với các quy định trong tiêu chuẩn này mới được xuất xưởng, khi xuất xưởng đui đèn phải có kèm theo phiếu chứng nhận phẩm chất của sản phẩm.
3.19. Thử xuất xưởng
a) Trong mỗi loạt sản phẩm để giao hàng lấy ra 0,2% nhưng không được ít hơn 20 cái để thử.
b) Nội dung thử xuất xưởng bao gồm các điều 2.3, 2.8, 2.15 và 2.19 trong tiêu chuẩn này.
c) Tất cả các mẫu lấy ra để thử đều phải phù hợp các yêu cầu của tiêu chuẩn này. Nếu có một mẫu không đạt bất kỳ điều nào thì phải lấy lại với số lượng gấp đôi trong loạt sản phẩm đó và thử lại điều chưa đạt. Nếu toàn bộ mẫu thử trong đợt lấy mới này đều đạt yêu cầu thì loạt sản phẩm đó được coi là đạt tiêu chuẩn, nhưng nếu lại có một mẫu không đạt thì loạt sản phẩm đó coi là không đạt tiêu chuẩn.
Những sản phẩm không đạt tiêu chuẩn thì phải sửa lại, nếu sửa không được thì bỏ.
d) Bản thân các mẫu thử nếu đạt tiêu chuẩn thì cũng được coi là thành phẩm xuất xưởng.
3.20. Thử điển hình
a) Thử điển hình được tiến hành khi có một trong các trường hợp sau đây:
– Sản phẩm mới chế tạo thử.
– Khi thiết kế công nghệ hoặc nguyên liệu có sự thay đổi lớn.
– Khi sản xuất lại những sản phẩm không thường xuyên sản xuất.
– Với các sản phẩm sản xuất thường xuyên hoặc hàng loạt lớn thì định kỳ thử ít nhất nửa năm một lần.
b) Nội dung thử điển hình bao gồm tất cả các điều quy định trong tiêu chuẩn này.
c) Mẫu thử điển hình chia làm 6 nhóm: từ nhóm 1 đến 4 thử trên sản phẩm; nhóm 5 và 6 thử trên chi tiết. Số lượng cần thử ít nhất là 5 cái.
Cách thử theo thứ tự sau:
– Nhóm 1 thử các điều: 2.8, 2.9, 2.18, 2.11, 2.7.
– Nhóm 2 thử các điều: 2.20, 2.3, 2.4, 2.5, 2.22 và 2.13.
– Nhóm 3 thử các điều: 1.3, 1.4, 1.5, 2.17, 2.21, 2.6 và 2.10.
– Nhóm 4 thử các điều: 2.16 và 2.12.
– Nhóm 5 thử điều 2.14.
– Nhóm 6 thử điều 2.15.
d) Những mẫu thử sau khi thử điển hình không được coi là thương phẩm để giao hàng.
3.21. Nếu trong khi thử điển hình có một mẫu không đạt một điều bất kỳ nào thì phải thử lại điều đó với số lượng gấp đôi. Nếu lại có một mẫu không đạt thì loạt sản phẩm đó coi là không đạt tiêu chuẩn.
3.22. Khi giao hàng, thủ tục nghiệm thu căn cứ theo các quy định về thử xuất xưởng với số lượng 0,1% lấy ra từ số sản phẩm sẽ giao nhưng không được ít hơn 20 cái.
Nếu khách hàng có nghi vấn về chất lượng của sản phẩm thì có quyền yêu cầu kiểm tra lại một phần hoặc toàn bộ các quy định trong thử điển hình với số lượng nhiều nhất không quá 30 cái, nhưng không được ít hơn 5 cái. Trong khi thử nếu có một mẫu thử không phù hợp yêu cầu của bất kỳ điều nào trong tiêu chuẩn này thì xử lý theo quy định ở điều 3.19 c.
4. GHI NHÃN, BAO GÓI, VẬN CHUYỂN VÀ BẢO QUẢN
4.1. Trên mỗi sản phẩm phải ghi đầy đủ và rõ ràng các đề mục sau:
a) Tên nhà máy sản xuất hoặc ký hiệu thương phẩm
b) Dòng điện làm việc lớn nhất (A)
c) Điện áp làm việc lớn nhất (V)
4.2. Đui đèn xếp trong các ô của hộp bìa cứng, trong hộp có kèm theo phiếu chứng nhận phẩm chất; mặt ngoài hộp có ghi nhãn theo quy định trong điều 4.1 và tên gọi, quy cách của sản phẩm.
4.3. Hộp đựng đui đèn lại được đóng vào hòm gỗ, hòm gỗ phải đạt các yêu cầu sau:
a) Quanh hòm lót giấy chống ẩm
b) Khối lượng thô của hòm không quá 40 kg.
c) Trong mỗi hòm phải có phiếu bao gói trong đó ghi đầy đủ các mục như tên sản phẩm, quy cách, số lượng, ngày bao gói và tên người bao gói v.v…
d) Nếu khách hàng đồng ý, có thể thay hòm gỗ bằng hòm bìa cứng chống ẩm hoặc bằng vật liệu khác nhưng phải đảm bảo trong quá trình vận chuyển không làm hư hỏng sản phẩm.
4.4. Bên ngoài hòm dùng sơn hoặc mực không phai ghi rõ các mục sau:
a) Tên sản phẩm, quy cách và số lượng
b) Tên nhà máy sản xuất
c) Tên người hoặc đơn vị và địa chỉ nơi nhận hàng
d) Khối lượng thô của hòm (kg)
e) Kích thước ngoài của hòm: dài x rộng x cao (cm)
g) Các ký hiệu cần chú ý như dễ vỡ, tránh nước, chiều quay lên v.v…
h) Ngày đóng hòm
4.5. Trong quá trình vận chuyển tránh va đập, rơi vỡ hoặc để mưa ướt.
4.6. Đui đèn được bảo quản trong kho thoáng, khô ráo, không có bụi bẩn và các chất ăn mòn.
PHỤ LỤC
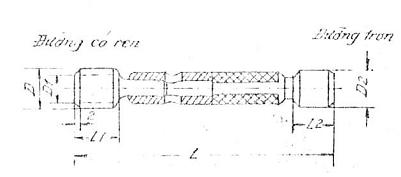
Hình 12
mm Bảng 12
Ký hiệu
|
Dưỡng có ren
|
Kích thước danh nghĩa và dung sai chế tạo
|
Độ mòn cho phép
D và D1
|
D
|
D1
|
t
|
r
|
L1
|
E 10
|
9,61+0,03
|
8,59+0,03
|
1,814 ± 0,015
|
0,531
|
10
|
– 0,02
|
E 14
|
13,97+0,04
|
12,37+0,04
|
2,822 ± 0,015
|
0,822
|
14
|
– 0,02
|
E 27
|
26,55+0,06
|
24,36+0,06
|
3,629 ± 0,02
|
1,025
|
18
|
– 0,03
|
E 40
|
39,60+0,09
|
36,00+0,09
|
6,359 ± 0,02
|
1,850
|
28
|
– 0,04
|
mm Bảng 13
Ký hiệu
|
Dưỡng trơn
|
Kích thước danh nghĩa và dung sai chế tạo
|
D2
|
L2
|
L
|
E 10
|
8,76 ± 0,008
|
9
|
79
|
E 14
|
12,56 ± 0,009
|
10
|
94
|
E 27
|
24,66 ± 0,010
|
16
|
130
|
E 40
|
36,45 ± 0,012
|
20
|
156
|
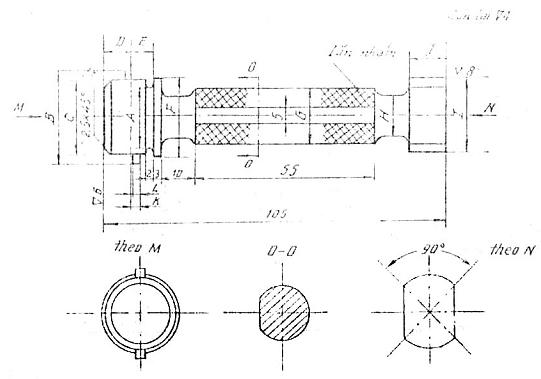
Hình 13
Bảng 14
Ký hiệu kích thước
|
1 B9
|
1 B15
2 B15
|
1 B 15 A
2 B 15 A
|
2 B 22
|
A
|
F 7
|
F 14
|
F 14
|
F 18
|
B
|
11+0,3
|
18,3+0,4
|
18,3+0,4
|
27,6+0,5
|
C
|
F 9,35-0,01
|
F 15,3-0,01
|
F 15,3-0,01
|
F 22,2-0,01
|
D
|
6,7-0,05
|
8-0,05
|
8-0,05
|
8,8-0,05
|
E
|
4,4+0,1
|
6+0,1
|
8+0,1
|
6,2+0,1
|
F
|
F 10,5+0,5
|
F 16,5+0,5
|
F 16,5+0,5
|
F 23,5+0,5
|
G
|
F 9,5
|
F 12
|
F 12
|
F 16
|
H
|
F 5,5
|
F 10
|
F 10
|
F 12
|
I
|
F 9,45+0,01
|
F 15,5+0,01
|
F 15,5+0,01
|
F 22,5+0,01
|
J
|
7,5+1
|
9,5+1
|
9,5+1
|
11,5+1
|
K
|
0
|
0
|
3,4-0,01
|
0
|
L
|
F 0,18+0,04
|
F 2,5+0,04
|
F 2,5+0,04
|
F 2,5+0,04
|
Độ mòn cho phép
|
C
I
|
– 0,02
– 0,02
|
– 0,03
– 0,02
|
– 0,03
– 0,02
|
– 0,03
– 0,02
|
|
|
|
|
|
|